ZINC
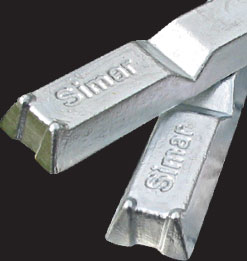
DONDE SE OBTIENE:
Los cinco primeros países productores de Zinc (China, Australia, Perú, Estados Unidos y Canadá) contribuyen con alrededor del 68.5% de todo este metal a nivel mundial. Su producción se ha incrementado de forma sustancial en los últimos 50 años, pasando de 2 millones de TM en 1952 a 11 millones de TM para el año 2008, lo que podría ser explicado por su mayor demanda, sobre todo del sector construcción (especialmente por el crecimiento mostrado en los últimos diez años por parte de China e India).
-CARACTERISTICAS: El zinc es un metal, a veces clasificado como metal de transición aunque estrictamente no lo sea, ya que tanto el metal como su especie dipositiva presentan el conjunto orbital completo. Este elemento presenta cierto parecido con el magnesio, y con el cadmio de su grupo, pero del mercurio se aparta mucho por las singulares propiedades físicas y químicas de éste (contracción lantánida y potentes efectos relativistas sobre orbitales de enlace). Es el vigésimo tercer elemento más abundante en la Tierra y una de sus aplicaciones más importantes es el galvanizado del acero. Hay que destacar que es un elemento químico esencial. Es un metal de color blanco azulado que arde en aire con llama verde azulada. El aire seco no le ataca pero en presencia de humedad se forma una capa superficial de óxido o carbonato básico que aísla al metal y lo protege de la corrosión. Prácticamente el único estado de oxidación que presenta es el +2. En el año 2004 se publicó en la revista Science el primer y único compuesto conocido de zinc en estado de oxidación +1, basado en un complejo organometálico con el ligando pentametilciclopentadieno. Reacciona con ácidos no oxidantes pasando al estado de oxidación +2 y liberando hidrógeno y puede disolverse en bases y ácido acético. El metal presenta una gran resistencia a la deformación plástica en frío que disminuye en caliente, lo que obliga a laminarlo por encima de los 100 °C. No se puede endurecer por acritud y presenta el fenómeno de fluencia a temperatura ambiente —al contrario que la mayoría de los metales y aleaciones— y pequeñas cargas el más importante..
-ALIACIONES: Las aleaciones más empleadas son las de aluminio (3,5-4,5%, Zamak; 11-13%, Zn-Al-Cu-Mg; 22%, Prestal, aleación que presenta superplasticidad) y cobre (alrededor del 1%) que mejoran las características mecánicas del zinc y su aptitud al moldeo. Es componente minoritario en aleaciones diversas, principalmente de cobre como latones (3 a 45% de zinc), alpacas (Cu-Ni-Zn) y bronces (Cu-Sn) de moldeo
-APLICACIONES: La principal aplicación del zinc —cerca del 50% del consumo anual— es el galvanizado del acero para protegerlo de la corrosión, protección efectiva incluso cuando se agrieta el recubrimiento ya que el zinc actúa como ánodo de sacrificio. Otros usos incluyen * Baterías de Zn-AgO usadas en la industria aeroespacial para misiles y cápsulas espaciales por su óptimo rendimiento por unidad de peso y baterías zinc-aire para computadoras portátiles. * Piezas de fundición inyectada en la industria de automoción. * Metalurgia de metales preciosos y eliminación de la plata del plomo.
-PROCESO PARA LA OBTENCIÓN DE ZINC: Recepción y almacenamiento de concentrados La principal materia prima de la fábrica de zinc está constituida por concentrados de sulfuro de zinc, procedentes de diferentes minas. Además de los concentrados sulfurados de zinc, se recibe la calcine Tostación y depuración de gases La tostación del concentrado se realiza en tres hornos, del tipo denominado de lecho fluido, cuyas capacidades de tostación son 300, 400, y 850 toneladas diarias de concentrados. En esta fase, el concentrado se tuesta con aire, formándose óxido de zinc (ZnO), denominado calcine, y dióxido de azufre gaseoso (SO2), que posteriormente se transforma en ácido sulfúrico (H2SO4) una vez enfriado y purificado el gas que sale de los hornos de tostación. Asimismo se origina vapor de agua que se emplea para la autogeneración de energía eléctrica así como fuente de calor en las etapas de lixiviación y purificación. Las diversas fracciones de calcine, tras ser refrigeradas y, en su caso, molidas, se transportan a unos silos de almacenamiento. El gas exento de calcine es tratado en torres de lavado para eliminar los componentes que puedan interferir en la producción de ácido sulfúrico. Igualmente se elimina el agua que pudiera ser arrastrada con la corriente gaseosa en los denominados precipitadores electrostáticos de gas de húmedo. Seguidamente el gas se envía a las plantas de ácido sulfúrico. Plantas de ácido sulfúrico El SO2 contenido en la corriente de gas impuro procedente del horno de tostación, se transforma en primer lugar en trióxido de azufre, debido a la reacción con el oxígeno en la torre de catálisis. Posteriormente, en la denominada torre de absorción intermedia, el trióxido de azufre resultante se absorbe en ácido sulfúrico del 99% de concentración, transformándose en ácido sulfúrico concentrado apto para uso en todo tipo de industrias, ya que las instalaciones están dotadas de un sistema de depuración de gases que permite la eliminación del mercurio, con carácter previo a su entrada en la planta de ácido. Lixiviación El zinc y los otros metales contenidos en la calcine se disuelven en ácido sulfúrico diluido, en dos etapas de lixiviación: lixiviación neutra y lixiviación ácida. En la etapa de lixiviación neutra se disuelve la mayor parte de la calcine, excepto las ferritas de zinc (óxido de hierro y zinc) en ella contenidas. Mediante la utilización de espesadores se separan los sólidos no disueltos de la disolución de sulfato de zinc. La disolución clarificada se envía a la etapa de purificación, mientras que los sólidos no disueltos se someten a la etapa de lixiviación ácida. La lixiviación ácida se realiza a una temperatura próxima a la de ebullición. De esta forma, se disuelven todos los metales excepto los que forman compuestos insolubles en medio sulfúrico, como el plomo, calcio y sílice. La disolución así obtenida se somete a un proceso de hidrólisis, tras el que se forma un sulfato básico de hierro insoluble llamado jarosita, que en unión de los metales no disueltos en esta segunda etapa constituyen el residuo final del proceso. Este residuo, después de una decantación en espesadores y posterior filtración, es enviado por bombeo a la balsa de residuos. Purificación La disolución de sulfato de zinc procedentes de la etapa de lixiviación neutra se trata mediante un proceso continuo realizado en dos etapas, para eliminar otros metales disueltos, como el cobre, el cadmio o el cobalto, que se recuperan como subproductos. Una vez realizada la filtración, la disolución de sulfato de zinc se enfría mediante torres de refrigeración y se bombea al tanque de almacenamiento de electrolito. Electrólisis El departamento de electrólisis engloba tres salas de operaciones, dos de ellas con una capacidad de 100.000 toneladas anuales y cátodos de tamaño estándar y arrancado semiautomático, y una tercera sala, puesta en funcionamiento el 14 de mayo de 1991, con una capacidad de 110.000 Tm. anuales, que está totalmente automatizada y sus controles se llevan a cabo mediante proceso electrónico. Esta sala se realizó mediante la aplicación de tecnología propia desarrollada por Asturiana de Zinc, S.A., y está considerada como una de las más modernas y de mayor eficiencia productiva del mundo. En esta fase del proceso, se produce el paso de una corriente eléctrica a través de la disolución purificada de sulfato de zinc, originándose el zinc metálico puro, que se deposita sobre laminas de zinc resultantes se arrancan automáticamente y son transportadas para su fusión y colado. Fusión y colada Las láminas de zinc producidas por electrólisis son fundidas en hornos de inducción eléctrica. Una vez fundido el zinc, se envía a las maquinas de colada con el objeto de producir las diversas formas comerciales de lingote que requiere el mercado. En el mismo departamento existen varios hornos en los que el zinc se combina con otros metales para producir aleaciones para fundición a presión, colada por gravedad, galvanización, laminación y otros. Los distintos lingotes que se producen, tanto de zinc como de las distintas aleaciones, se apilan, pesan y empaquetan de forma automática. Todos los hornos se encuentran conectados a un sistema de depuración de gases para eliminar el polvo que éstos contienen antes de emitirse a la atmósfera. Su actividad consiste en la tostación de concentrados de zinc (sulfuro de zinc), obteniendo como productos finales óxido de zinc (calcine) y anhídrido sulfuroso líquido. Proceso productivo El concentrado de zinc procedente de las mina, previamente a su tostación, sufre un secado y molienda . La tostación de la blenda se realiza en un horno Flash a temperaturas de unos 1.000C, pudiendo tratar al día entre 190 y 200 Tm., con un volumen entre 26.000 y 28.000 m3/h. El residuo sólido del proceso es el óxido de zinc (calcine), que se envía a la planta de zinc electrolítico. Los gases procedentes de la tostación se concentran eliminando el oxígeno y el nitrógeno, que son los gases que lo diluyen. Este proceso se fundamenta en la absorción selectiva que la dimentilanilina (DMA) tiene sobre el anhídrido sulfuroso, dejando libre el resto de los gases, que se realiza en una torre de absorción del anhídrido sulfuroso y la DMA, en una segunda torre, mediante aporte calorífico. El anhídrido sulfuroso líquido obtenido se seca con ácido licuado posteriormente mediante una batería de compresores y condensadores antes de almacenarlos para su comercialización. La producción diaria de la planta es de aproximadamente 165Tm. de calcine y 105Tm. de anhídrido sulfuroso líquido, con una pureza superior al 99,95%.
-LOCALISACIÓN DE MINAS DE ZINC:
http://www.unctad.org/infocomm/espagnol/zinc/empresas.htm